At so-i, we practice "Aizome", traditional Japanese indigo dyeing, using an ancient method called "Aka-hakkō-date" (natural lye fermentation).
The dye is made entirely from natural materials: fermented indigo leaves (sukumo), wood ash lye, oyster shell lime, and wheat bran—no chemicals involved.
The indigo in our vats gently sways, alive and constantly changing.
It cannot be fully controlled by human will; it responds to the mood and care of the person tending it.
Its color shifts day by day, offering endless moments of surprise and discovery.
We invite you to experience the living blue of so-i—a shade born from nature, not manufactured, but nurtured.
-
Sukumo (fermented indigo leaves)
Sukumo, the key ingredient in the lye fermentation method of indigo dyeing, is a natural dye made by fermenting indigo leaves.
After being harvested in the summer, the leaves are dried and then piled into a fermentation bed.
Water is sprinkled and the pile is turned regularly to encourage fermentation.The entire process takes about 120 days, requiring patience and care.
Through fermentation and aging, sukumo develops the deep qualities needed to create beautiful shades of indigo. -
Indigo Fermentation
High-quality lye is essential for the natural fermentation method (Aka-hakkō-date).
We use wood ash from Yamaguchi Prefecture to produce a clear, clean lye without impurities.
This lye is not only used in indigo vat preparation, but also for scouring and rinsing the fabric after dyeing.No chemicals are used in preparing the indigo dye vat—Ai-date, the process of building the indigo vat, relies solely on natural ingredients:
sukumo (fermented indigo leaves), wood ash lye, oyster shell lime, and wheat bran.
These materials are fermented together in a large clay vat to produce the indigo dye.After about ten days of careful fermentation, when a bloom known as the "ai no hana" (indigo flower) appears on the surface, the vat is ready for dyeing.
Inside the vat, the indigo is alive.
Each day we stir it gently, observe its condition, and tend to it with care—drawing out all the color that the sukumo has to offer.Once the indigo has given its color fully, it is returned to the fields and returned to the earth.
-
Dyeing
Fabrics and threads are repeatedly dipped into the indigo vat, allowing oxidation to develop the color and deepen its shade.
The dyeing method and number of dips vary depending on the material.We carefully maintain the indigo vat daily, monitoring its condition to ensure consistent dyeing.
Using techniques such as stencil dyeing and shibori (tie-dyeing), we can create a variety of patterns and designs. -
Water Rinse
We repeat cycles of rinsing with underground spring water and lye, followed by warm water washes.
This process removes impurities and any excess indigo that did not bond with the fabric or thread.It is a vital step that greatly contributes to the clarity and brilliance of the final color.
-
Finishing
The fabric and thread are sun-dried to draw out any remaining lye or impurities.
Exposure to sunlight also improves colorfastness.
By repeating cycles of rinsing and drying under the sun, we complete the finishing process.With the help of water, wind, and light, the indigo develops into a clear and vibrant blue.
In your daily life
At so-i, where we work with natural materials, every step in our process holds meaning and purpose.
With proper care, we believe the rich texture and character unique to natural indigo can be enjoyed for many years.
It is our hope that our creations will gently accompany and enrich your everyday life.
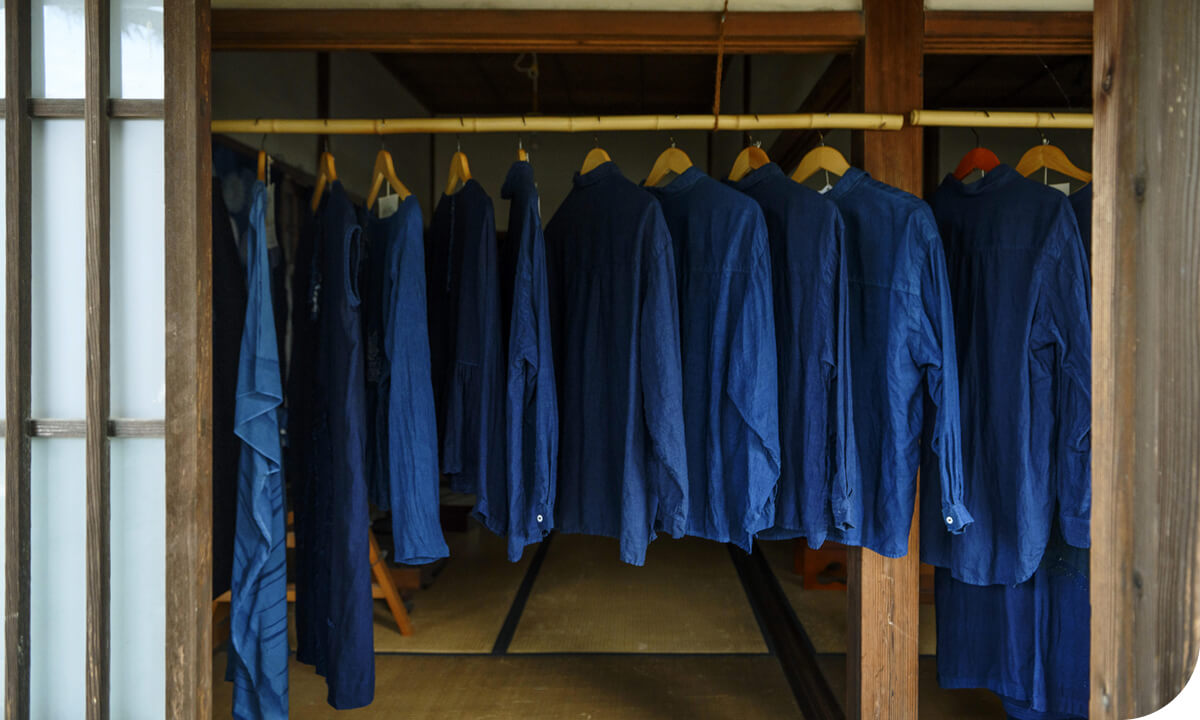